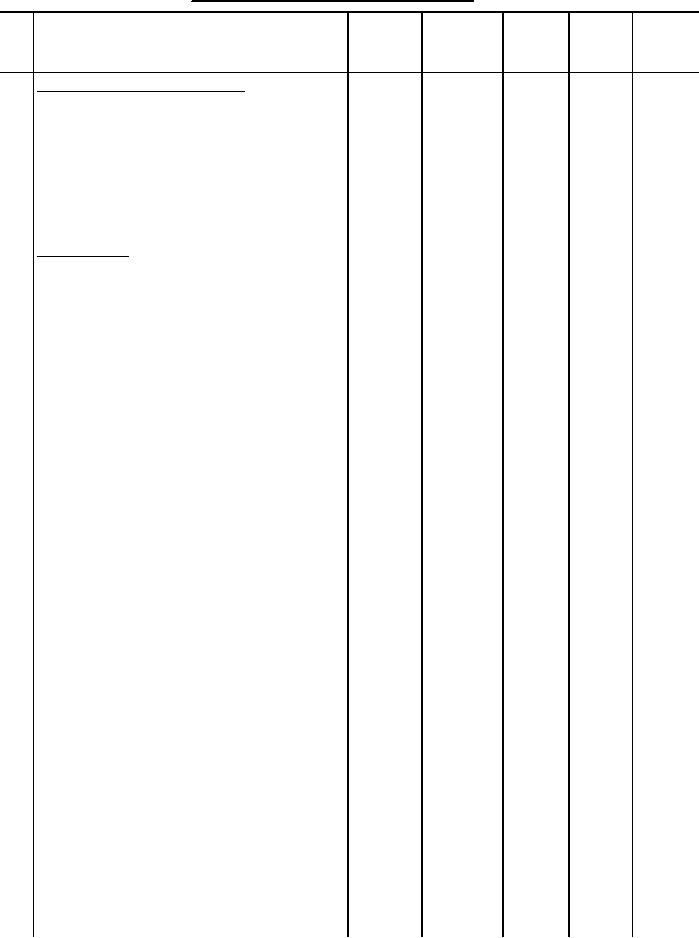
MIL-DTL-82168C(MC)
Manufacturing requirements - Continued.
TABLE I.
SEAM/
STCH
STCH
BOB/
NO
OPERATION
TYPE
TYPE
STCH/IN
NDL
LPR
5
(cont'd)
Make collar eyelet covers.
a. Turn under the side of the collar
301
EFa-1
12-16
A
A
eyelet cover and stitch 1/8 inch from
(each
the folded edges, catching the turned
side
under portions in the stitching.
edge)
b. Fold each cover in half, across
301
SSa-1
12-16
A
A
the width and seam 1/16 inch from the
folded side edges.
6
Make collar.
Finished appearance. The completed
collar shall finish smooth and flat
without distortion. Edges shall be
uniformly even.
a. The collar shall be made of one
ply of basic material, lining, twill
or plain weave polyester and cotton
buckram and one ply of mylar plastic.
b. Seam the plastic, polyester and
301
SSa-1
12-16
A
A
cotton buckram together 1/8 to 3/16
inch from all edges and trim the
polyester even with the edges of the
buckram. The polyester cloth shall
be positioned on the inside and the
plastic (mylar) on the outside.
c. Lap the upper edge of the
301
LSa-1
12-16
A
A
polyester side of the interlining
approximately 1/2 inch to the upper
edge of the outer ply. Seam together
1/4 inch from the raw edge of
interlining. The outer ply shall
extend not less than 3/4 inch at each
end.
d. Smoothly fold the outer ply over
Hand
2-3
the lower and upper edges of the
interlining. Tack the outer ply,
folded to the inside, at the lower
edges of the polyester from end to
end. Stitching shall not pass
through the outer ply of the collar.
e. Fold the ends of the outer ply to
Hand
2-3
the inside of the interlining and
tack to the polyester with overcast
stitching, turning under the upper
and lower edges sufficiently, so as
not to be visible in the finished
collar.
14
For Parts Inquires call Parts Hangar, Inc (727) 493-0744
© Copyright 2015 Integrated Publishing, Inc.
A Service Disabled Veteran Owned Small Business